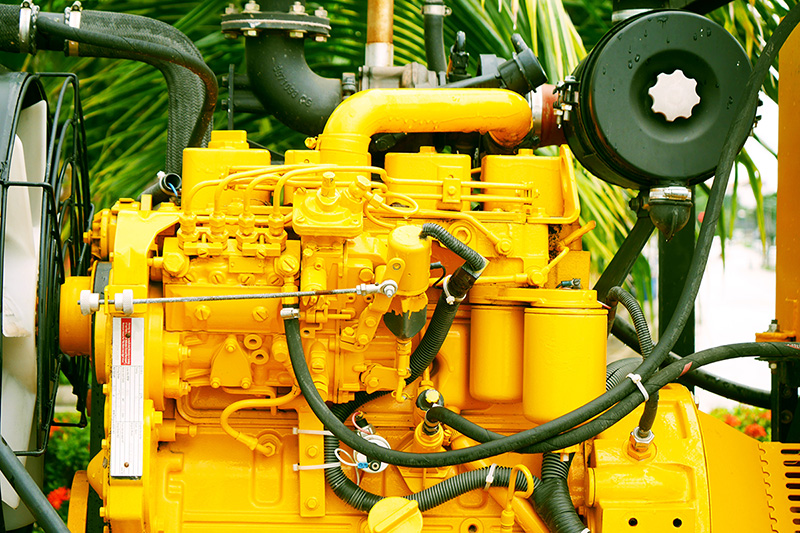
Mobile hydraulic systems are essential for the efficient operation of heavy machinery in industries like agriculture, construction, transportation, and mining. By harnessing the principles of fluid power, these systems deliver the strength, precision, and control required to perform tasks such as lifting, digging, and material handling. In this blog, we will take an in-depth look at how mobile hydraulic systems work, their key components, industry applications, and the latest innovations shaping the future of hydraulic technology.
What is mobile fluid power?
Mobile fluid power refers to the use of hydraulic and pneumatic systems in mobile equipment to convert mechanical energy into fluid energy and back into mechanical work. This power transfer allows for high power density and precise control, making it the ideal solution for heavy machinery that requires immense force to operate. From tractors and excavators to forklifts and mining trucks, mobile fluid power plays a crucial role in many sectors.
How does a mobile hydraulic system work?
Mobile hydraulic systems function by pressurizing hydraulic fluid within a closed circuit. This fluid is then directed by valves and control systems to actuators, which convert the hydraulic energy into mechanical motion. The process begins with a hydraulic pump that creates fluid flow under pressure, enabling the machinery to perform its tasks. Hydraulic actuators such as cylinders and motors then translate this fluid power into physical movement, enabling mobile equipment to lift, push, or move objects.
Key benefits of mobile hydraulic systems:
-
High Power Density: Mobile hydraulic systems can deliver significant force in a compact space, enabling smaller machinery to perform powerful tasks without the need for large, cumbersome engines.
-
Precise Control: Hydraulic systems offer fine-tuned control, making them ideal for applications that require accuracy, such as in construction machinery and agricultural equipment.
-
Energy Efficiency: Hydraulic systems can be more energy-efficient than mechanical or electrical systems, converting energy with minimal losses, which helps reduce fuel consumption and emissions.
-
Durability and Reliability: Mobile hydraulic systems are built to withstand extreme working conditions and heavy loads, making them reliable for long-term use in harsh environments.
Essential Components of Mobile Hydraulic Systems
To fully understand the operation of mobile hydraulic systems, it's important to familiarize yourself with the critical components that make these systems efficient and reliable.
Hydraulic Fluid
Hydraulic fluid is the lifeblood of any hydraulic system. This is a specialized oil formulated for lubricating properties, thermal stability, low compressibility, foam resistance, and ability to maintain consistent viscosity under different conditions. It transmits power and protects the system from wear and tear. The choice of hydraulic fluid depends on the application, with high-performance fluids offering longer life and better resistance to oxidation.
Hydraulic Pump
Often called the heart of the hydraulic system, the pump pressurizes the hydraulic fluid, generating the energy needed to power the system. Various types of pumps, such as gear pumps, vane pumps, and piston pumps, are used depending on the application. Piston pumps, for example, are commonly used in heavy-duty applications like construction equipment due to their ability to handle higher pressure and flow rates.
Hydraulic Actuators
Actuators are responsible for converting hydraulic pressure into mechanical action. There are two primary types of actuators: hydraulic cylinders (which produce linear motion) and hydraulic motors (which produce rotational motion). For example, in an excavator, the hydraulic cylinders extend and retract to move the arms and bucket, while hydraulic motors rotate the tracks and the upper structure (house).
Valves and Control Systems
Hydraulic valves and solenoids regulate the flow, direction, and pressure of fluid within the system. Directional control valves manage fluid paths, while pressure relief valves maintain safe operating limits, and proportional valves allow variable control for more precise adjustments. Unlike valves, which physically direct the fluid, solenoids are electromechanical devices that actuate valves, enabling remote or automated operation. Together, these components ensure smooth performance and precise control of mobile machinery.
Hydraulic Reservoir
The reservoir stores excess hydraulic fluid and plays a key role in maintaining pressure levels, cooling the fluid, and allowing air bubbles to escape. It ensures that the hydraulic system has a continuous supply of fluid, and its size is typically determined by the system's requirements.
Hydraulic Oil Coolers
Hydraulic oil coolers maintain optimal fluid temperatures by dissipating excess heat generated during system operation. They prevent overheating, which can degrade oil, damage seals, and reduce component lifespan. By ensuring stable temperatures, coolers improve system efficiency, extend equipment life, and reduce maintenance needs in demanding applications.
Filtration Systems
Contamination is one of the biggest threats to hydraulic systems. Filtration systems remove impurities like dirt, metal particles, and other debris that could damage system components. Regular filter maintenance is crucial for maintaining system performance and longevity. Some advanced filtration systems not only filter for contaminants but also separate water and air from the hydraulic fluid maintaining high fluid quality and purity.
Applications of Mobile Hydraulic Systems Across Industries
Mobile hydraulic systems are versatile and find applications across multiple industries. Here are some of the key applications:
Agriculture: Enhancing Farm Equipment Efficiency
In agriculture, hydraulic systems power tractors, harvesters, and other machinery, as well as control attachments like plows, harrows, and tillers. They provide precise control of equipment and implements, helping farmers maximize productivity and reduce manual labor.
Construction: Powering Heavy Machinery
Construction equipment like excavators, loaders, and cranes rely on hydraulic systems for power and precision. These systems enable efficient digging, lifting, and material handling, even in harsh conditions. For example, excavators use hydraulic cylinders to control arm and bucket movement, while hydraulic motors power track and upper structure (house) rotation for precise operation.
Material Handling: Lifting and Transporting Heavy Loads
Forklifts, conveyors, and other material handling equipment use hydraulic systems to lift and transport heavy loads with ease. In warehousing and distribution centers, hydraulics are critical for the efficient movement of goods, ensuring safety and productivity.
Mining and Off-Highway Vehicles
Mobile hydraulic systems power mining trucks, bulldozers, and other off-highway vehicles, enabling them to operate in harsh environments and handle massive loads. These systems must be robust and reliable to ensure uninterrupted operation in challenging conditions.
Transportation: Hydraulics in Trucks and Trailers
Hydraulic systems are essential for dump trucks, garbage trucks, and other transport vehicles that need to lift, tilt, or compact materials. These systems increase the functionality of vehicles, making them more versatile for a range of applications.
Maintaining and Optimizing Mobile Hydraulic Systems
Regular maintenance is essential for ensuring the long-term efficiency and reliability of mobile hydraulic systems. Key maintenance practices include:
- Fluid Checks and Replacement: Regularly monitor hydraulic fluid levels and replace the fluid as needed to prevent contamination and maintain optimal performance.
- Filter Maintenance: Change filters on a regular schedule to remove contaminants and extend the life of system components.
- Hydraulic Fluid Cooler Maintenance: Inspect and clean coolers regularly to ensure unrestricted airflow and prevent overheating.
- Hose and Seal Inspections: Check hoses and seals for signs of wear, leaks, or damage. Replacing worn parts promptly can prevent system failures and reduce downtime.
Emerging Trends in Mobile Hydraulic Systems
Mobile hydraulic systems are continuously evolving with new innovations that improve efficiency and performance:
Hybrid Hydraulic-Electric Systems
As industries move toward greener technologies, hybrid systems combining hydraulic and electric power are becoming more prevalent. These systems offer enhanced energy efficiency and lower emissions, particularly in mobile machinery used in urban environments.
Smart Hydraulics
Smart control systems, incorporating sensors and real-time data analytics, are improving the precision and responsiveness of hydraulic systems. These systems can automatically adjust fluid pressure and flow based on load conditions, improving both performance and energy efficiency.
Biodegradable Hydraulic Fluids
In response to environmental concerns, there is growing interest in biodegradable hydraulic fluids. These eco-friendly fluids minimize environmental impact in the event of a leak and are particularly suited for agriculture and forestry applications.
Energy-Efficient Pumps
Advances in pump technology are reducing energy consumption in hydraulic systems. Variable displacement pumps, for example, adjust their flow and pressure based on system needs, helping reduce energy use and operating costs.
Maximizing the Potential of Mobile Hydraulic Systems
Mobile hydraulic systems are the driving force behind many of today’s heavy machinery, delivering the power, precision, and efficiency needed for challenging industrial applications. By understanding their components, ensuring proper maintenance, and staying up-to-date with innovations, businesses can maximize the performance and lifespan of their equipment.
Need Help?
Contact your local Royal Brass and Hose sales representative or call us at 800-669-9650 to speak with a member of our Customer Service team at any of our locations across the Southern United States.