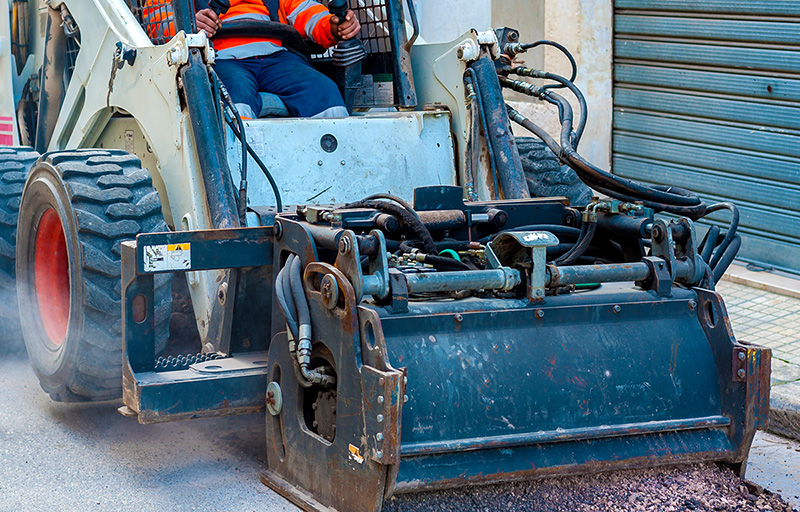
In this blog:
- What are flush face hydraulic quick disconnect couplers?
- How to identify the right flush face hydraulic quick disconnect coupler?
- Repairing flush face hydraulic quick disconnect couplers
- Common misconceptions about flush face hydraulic quick disconnect couplers
- Applications of flush face hydraulic quick disconnect couplers across industries
- Shop flush face hydraulic quick disconnects
In the dynamic landscape of hydraulic systems, flush face quick disconnect (QD) couplers stand out for enhancing system efficiency and reliability. This type of coupling offers rapid connection capabilities, minimal leakage, and ease of use. For those involved in the design, maintenance, or operation of hydraulic systems, it’s important to understand how to identify and properly use flush face QD couplers. Far from being mere connectors, these couplers are engineered solutions designed to ensure a tight, nearly leak-free seal between hoses or components in a hydraulic circuit. Knowledge of the couplers’s types, pressure ratings, and materials is key for optimizing hydraulic system performance and longevity. Additionally, understanding their quick connect and disconnect mechanisms can improve operational safety and efficiency.
What are flush face hydraulic quick disconnect couplers?
Flush face QD couplers are hydraulic couplings designed for quick and tool-free connection and disconnection of hydraulic lines. Their design significantly reduces fluid spillage during the connection and disconnection process. The "flush face" design ensures that the sealing surface of the couplers is smooth, which, unlike couplings with a protruding nose or indented seat, facilitates easy cleaning and reduces the risk of contamination.
The main components of a flush face QD coupler—the female part (socket) and the male part (plug)—form a secure seal when connected, essential for the hydraulic system's integrity and efficiency.
Key features of flush face QD couplers include:
-
Nearly Leak-Free Performance: While traditionally described as leak-free, it's more accurate to say they are nearly leak-free, with potential leakage rates significantly lower than those of poppet style couplings, ranging from approximately 0.03 to 0.15 ml (about 0.01 oz).
-
Easy to Clean: The flush face design simplifies the cleaning process, effectively reducing dirt and contamination risk in the hydraulic system.
-
Reduction of Air Introduction: These couplers are designed to minimize the introduction of air into the system, enhancing performance and reliability.
-
Higher Flow Rates: The design of flush face QD couplers allows for higher flow rates compared to other types of couplings, improving system efficiency.
-
Versatility: Employed across multiple industries for their reliability and ease of use, these couplers can withstand high pressures and are suitable for heavy-duty hydraulic applications.
How to identify the right flush face hydraulic quick disconnect coupler?
Selecting the correct hydraulic quick coupler helps ensure system efficiency and reliability. Consider the following factors when selecting a flush face QD coupler: inspecting coupler stampings, verifying compliance with standards (e.g., ISO 7241, ISO 16028), consulting manufacturer catalogs, measuring dimensions, using profile charts for identification, and double-checking specifications before ordering.
-
Inspecting Coupler Stampings: Begin by examining the coupler for any stampings or engravings. These markings often include the manufacturer's name, part number, and specifications such as size, series, or material. Stampings serve as the first clue to the coupler's compatibility and standards adherence.
-
Verifying Compliance with Standards: Using the stamping information, check if the coupler meets international standards like ISO 7241 (Series A and B) or ISO 16028 for flush face couplers. These standards ensure interchangeability and performance expectations.
-
Consulting Manufacturer Catalogs: Once you've identified the series or part number, refer to the manufacturer's catalog or website for detailed specifications, including dimensions, material composition, pressure ratings, and compatibility information. This step is important, especially for couplers with proprietary profiles.
-
Measuring and Comparing Dimensions: If stampings are unclear, measure key dimensions of the coupler, including the diameter of male and female parts, length, and thread size and type. Compare these measurements against manufacturer specifications to confirm the series and size.
-
Using Profile Charts for Identification: Profile charts are particularly useful for visual comparison, especially for standard-compliant couplers. Lay the coupler against a scaled drawing to verify its profile and size, ensuring accurate identification.
-
Checking Rear Thread Type for Spare Parts: When identifying a coupler for spare parts, pay close attention to the rear thread type, ensuring compatibility with your existing system.
Repairing & maintaining flush face hydraulic quick disconnect couplers
-
Diagnosis: Begin by diagnosing the issue. Common problems include leaks, inability to connect or disconnect, and damaged seals or valves. Inspection should include checking for visible damage, wear, and contamination.
-
Disassembly: Carefully disassemble the coupler, noting the position of each component. Use appropriate tools to avoid damaging the parts. It's essential to work in a clean environment to prevent contaminating the coupler internals.
-
Cleaning and Inspection: Clean all disassembled parts with a suitable solvent and inspect them for wear, damage, or corrosion. Pay special attention to sealing surfaces, as these are critical for nearly leak-free performance.
-
Replacing Worn or Damaged Parts: Replace any components that show signs of wear or damage. It is often advisable to replace seals and O-rings, even if they appear undamaged, to ensure the best possible seal upon reassembly.
-
Reassembly: Reassemble the coupler according to the manufacturer's instructions. Ensure that all seals are correctly positioned and that all components are securely tightened. Lubricate parts as recommended by the manufacturer to facilitate smooth operation.
-
Testing: After reassembly, test the coupler under controlled conditions to ensure it operates correctly and is leak-free. This may involve connecting the coupler to a hydraulic system and observing its performance under pressure.
-
Maintenance: Regular maintenance is key to extending the life of flush face QD couplers. This includes routine cleaning, inspection, and immediate replacement or repair of damaged components.
Check out our flush face accessory and repair products:
- Flush Face Molded Rubber Dust Cap
- Flush Face Seal Kit
- Flush Face Nitrile Dust Plug
- Flush Face Nitrile Dust Cap
- Flush Face Polyurethane Colored Band
- Blue Wolf All Purpose Cleaner and Degreaser
Common misconceptions about flush face hydraulic quick disconnect couplers
Misconception 1: "One Size Fits All"
The belief that any flush face QD coupler can fit any hydraulic system is a widespread misconception. Hydraulic systems are designed with specific requirements, including pressure ratings, flow rates, and connection sizes. A coupler that fits physically may not be suitable operationally if it doesn't match the system's specifications. This misconception can lead to inefficient system performance, increased wear and tear, or even system failure. It's imperative to select couplers based on the exact requirements of the system, considering factors such as the operating pressure, flow requirements, and the physical dimensions of the coupler.
Misconception 2: Brand Interchangeability
Another common misunderstanding is assuming that couplers from different manufacturers are interchangeable if they appear similar. While many flush face QD couplers are designed to comply with international standards like ISO 16028, ensuring some level of interchangeability, not all products strictly adhere to these specifications. Variations in manufacturing tolerances, material properties, and seal designs can lead to compatibility issues, even among seemingly identical couplers. Before substituting couplers from different brands, verify that they are fully compatible in all aspects critical to the system's operation.
Misconception 3: Ignoring Profile Variations
The external appearance of a coupler can be deceiving. Two couplers may look alike but have different internal profiles, leading to improper sealing and connection issues. The profile refers to the shape and design of the coupler's connecting ends, which must match precisely to form a secure and leak-free connection. Ignoring these variations can result in leaks, contamination, and reduced system efficiency. Always ensure that the coupler profiles match exactly, using manufacturer's catalogs or profile charts for verification.
Misconception 4: Overlooking the Importance of Stampings
Stampings on a flush face QD coupler provide imperative information, including the manufacturer's name, part number, and specifications like size, pressure rating, and material. Disregarding this information can lead to selecting the wrong coupler, incompatible with the system's requirements. Misinterpretation or oversight of these details can result in operational inefficiencies, increased downtime, and higher replacement costs. It is useful to read and understand the stampings to ensure that the selected coupler meets the system's specifications fully.
Applications of flush face hydraulic quick disconnect couplers across industries
Construction and Heavy Machinery
In the construction industry, hydraulic systems power a wide range of equipment, from excavators and bulldozers to cranes and loaders. Flush face QD couplers are used extensively to quickly change hydraulic attachments, ensuring that machinery can adapt to different tasks with minimal downtime.
Wheel loaders and skid steer loaders use flush face QD couplers to change attachments like forks, buckets, and snowplows quickly. This adaptability is key for meeting the diverse needs of construction projects, from material handling to site clearing, while ensuring minimal downtime and preventing fluid leakage in sensitive environments.
For an excavator operating on a construction site, flush face QD couplers enable the swift exchange of attachments such as buckets, hammers, and rippers. This versatility allows a single machine to perform multiple tasks throughout the day, from digging trenches to breaking concrete. The nearly leak-free performance of these couplers minimizes the risk of hydraulic oil spills, which can contaminate the site.
Cranes benefit from flush face QD couplers in their hydraulic systems for quick setup adjustments and attachment changes, such as switching between different lifting hooks or grabs. This capability is essential for maintaining project timelines and adhering to strict safety and environmental standards, especially in urban construction environments where space and time are limited.
Agriculture
Agricultural machinery can benefit from the quick-connect capabilities of flush face QD couplings. Their design allows for rapid tool and implement changes with minimal spillage. Farming operations will see increased versatility and efficiency, while reducing the risk of contaminating the soil; protecting the land and crops.
In modern farming, tractors equipped with flush face QD couplers can easily switch between implements such as plows, seed drills, and sprayers. This quick-change capability enhances a tractor's utility, allowing for efficient transitions between planting, cultivating, and harvesting operations without soil contamination from hydraulic leaks.
For harvesters, the use of flush face QD couplers facilitates the rapid attachment and detachment of different harvesting heads, suitable for crops ranging from wheat and corn to cotton and soybeans. This flexibility is vital for maximizing the efficiency of harvest operations and reducing the risk of hydraulic fluid leaking onto the crops.
Mobile irrigation systems benefit from flush face QD couplers by enabling quick connections to water sources and distribution equipment. The couplers' design minimizes leaks and contamination, ensuring that water used for irrigation remains clean and that the system is easy to reconfigure or move as needed.
Manufacturing and Industrial
In manufacturing settings, hydraulic systems are integral to production lines, presses, and automated machinery. Flush face QD couplers facilitate quick maintenance and mold changes, minimizing production downtime. Their high flow rates improve machine efficiency, while the ease of cleaning helps maintain a contaminant-free environment, crucial for high-precision manufacturing processes.
In the automotive industry, flush face QD couplers are used in automated assembly lines for quick tool changes and maintenance. For example, robotic arms equipped with these couplers can switch between welding, painting, and assembly tools rapidly, minimizing downtime and maintaining high production rates.
In the plastics manufacturing sector, flush face QD couplers allow for quick mold changes in injection molding machines. This capability significantly reduces downtime between production runs, essential for meeting tight production schedules and maintaining a contaminant-free environment critical for producing high-quality plastic parts.
Metal forming presses use flush face QD couplers to facilitate rapid die changes and maintenance operations. The high flow rates supported by these couplers enhance the efficiency of hydraulic systems by enabling faster cycle times and reducing the risk of contamination during die changes. Both being essential aspects for maintaining precision and product quality.
Conclusion
Incorporating flush face QD couplers into hydraulic systems not only facilitates operational excellence, but also promotes sustainability by minimizing spillage and contamination risks. Their robust design and advanced sealing technology are key to achieving a cleaner work environment and reducing the ecological footprint of hydraulic applications. By adhering to the guidelines and best practices outlined in this guide, professionals can ensure that their hydraulic systems are not only optimized for peak performance but are also aligned with the evolving standards of environmental responsibility and worker safety.
Shop flush face hydraulic quick disconnects, accessories, and repair products
- Flush Face Socket with Female Threads
- Flush Face Socket with Male Threads
- Flush Face Socket with Female Threads - Blister Pack
- Flush Face Plug with Female Threads - Blister Pack
- Flush Face Molded Rubber Dust Cap
- Flush Face Seal Kit
- Flush Face Nitrile Dust Plug
- Flush Face Nitrile Dust Cap
- Flush Face Polyurethane Colored Band
- Blue Wolf All Purpose Cleaner and Degreaser
Need help with your flush face hydraulic quick disconnects?
When it comes to quick disconnects, we’re trusted experts. Contact us or call 1-800-669-9650 to speak with a member of our customer service team at any of our 11 locations (Knoxville, TN; Marietta, GA; Orlando, FL; Charlotte, NC; Little Rock, AR; Fort Worth, TX; Benton, IL; Madisonville, KY; Princeton, WV; Birmingham, AL; Calvert City, KY).