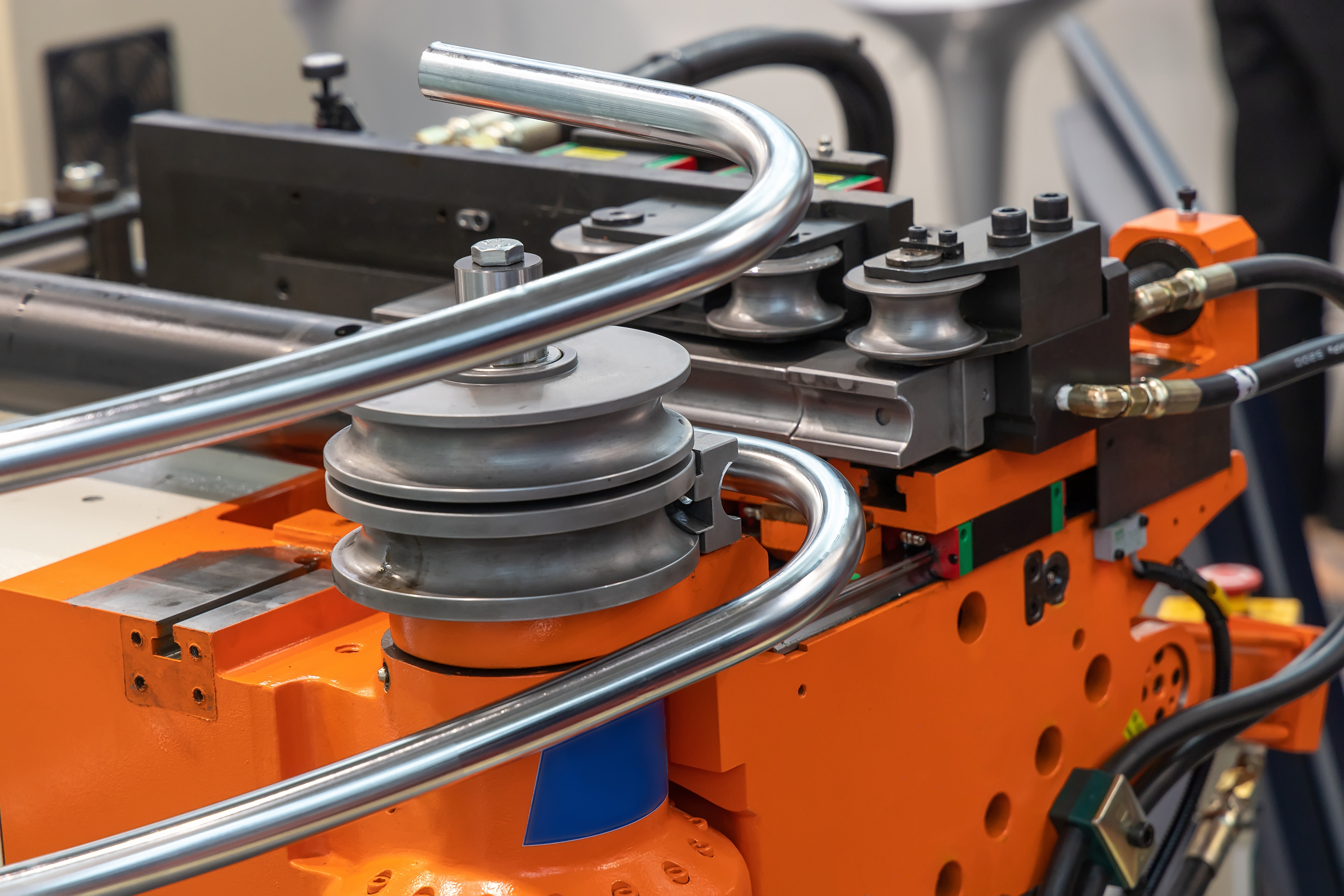
Tube bending and assembly play a critical role in numerous industries, from automotive to aerospace. Whether you need to create intricate piping systems or simple tube configurations, understanding the tube bending process is essential. In this blog, we'll delve into the ins and outs of tube bending and assembly, highlighting the key aspects you need to know if you're seeking top-notch tube assembling services.
What is tube bending?
Tube bending consists of a series of manufacturing processes that alter the shape of a pipe or tube to create the desired geometry or features that meet specific requirements. In the process, tube stock is loaded into a bending machine which uses mechanical forces to push the tube against dies and rollers that cause the tube to conform to a shape. Tube bending can be done in a wide selection of metal tubing and pipe materials, including steel, stainless steel, aluminum, brass, copper, and titanium.
Curious how custom tube bending is leveraged in the real world? Here’s an example of an automative OEM.
Custom tube assembly for the automotive industry
An automotive OEM needs to design a new fuel delivery system for their latest line of high-performance vehicles. The system requires complex tube configurations to ensure optimal fuel flow, minimize emissions, and fit within the compact engine compartments of modern cars. Off-the-shelf tube assemblies are inadequate due to the specific geometric and performance requirements of the project.
To meet these challenges, the OEM partners with a vendor or distributor who specializes in tube bending for industrial applications.
Here’s how the project will typically go:
- Design and Engineering Collaboration
-
Collaborative Design Process: The OEM’s engineers work closely with the tube bending service provider to develop a custom design for the fuel delivery system. This involves creating detailed CAD models and simulations to ensure optimal fuel flow and system performance.
-
Prototyping and Testing: Initial prototypes are produced using advanced CNC bending machines. These prototypes undergo rigorous testing for flow dynamics, pressure resistance, and durability, allowing for iterative improvements before full-scale production.
-
- Customization and Flexibility
-
Complex Geometries: The fuel delivery system requires tubes with intricate bends and precise angles to navigate the limited space within the engine compartment. bending machines enable the creation of these complex shapes with high precision, ensuring a perfect fit.
-
Material Selection: Given the need for high durability and resistance to corrosion, materials such as stainless steel and aluminum may be chosen. The service provider’s expertise in bending these materials ensures that the tubes maintained their integrity and performance characteristics.
-
- Precision and Efficiency
-
Exact Specifications: CNC bending technology allows for each tube to meet exact specifications, reducing the risk of errors and ensuring consistency across all units.
-
Streamlined Production: The automated bending process significantly reduces production time. This efficiency enables the OEM to meet tight production schedules and quickly adapt to changes in design requirements.
-
-
Quality Assurance and Reliability
-
Stringent Quality Control: Each custom tube assembly undergoes comprehensive quality control and dimensional checks, ensuring that every component meets the stringent quality standards required for high-performance automotive applications.
-
Regulatory Compliance: The custom tube assemblies are designed to comply with industry regulations and environmental standards, ensuring that the final product is market ready.
-
Why OEMs trust Royal Brass and Hose for custom tube assembly
With Royal Brass and Hose, OEMs can successfully develop a reliable tubing system tailored to their specific requirements. The benefits included:
-
Optimized Flow: Custom tube design ensures efficient delivery of fluids or gases.
-
Compact and Efficient Design: The precise bending and assembly allows the system to fit seamlessly within the tight confines of your application, meeting space constraints without compromising functionality.
-
Cost Savings: Royal Brass and Hose can process orders large and small quickly. Our high-quality output minimizes rework and material wastage, resulting in significant cost savings. Plus, our experts will help you determine the right material and solution for your application, so you get it right the first time.
The need for precise, efficient, and reliable components in a tube or pipe assembly is critical for production or use of equipment. By partnering with a specialized tube bending provider like Royal Brass and Hose, OEMs can achieve tailored solutions that enhance product performance, meet specific design criteria, and maintain a competitive edge in the market.
Looking for tube assembling services?
Proper tube assembling is crucial for ensuring the integrity and performance of your tubing systems. By employing skilled professionals for your tube assembly needs, you can ensure that each component is perfectly aligned, securely connected, and meets industry standards. Contact us or call 1-800-669-9650 to speak with a member of our customer service team at any of our 11 locations (Knoxville, TN; Marietta, GA; Orlando, FL; Charlotte, NC; Little Rock, AR; Fort Worth, TX; Benton, IL; Madisonville, KY; Princeton, WV; Birmingham, AL; Calvert City, KY).