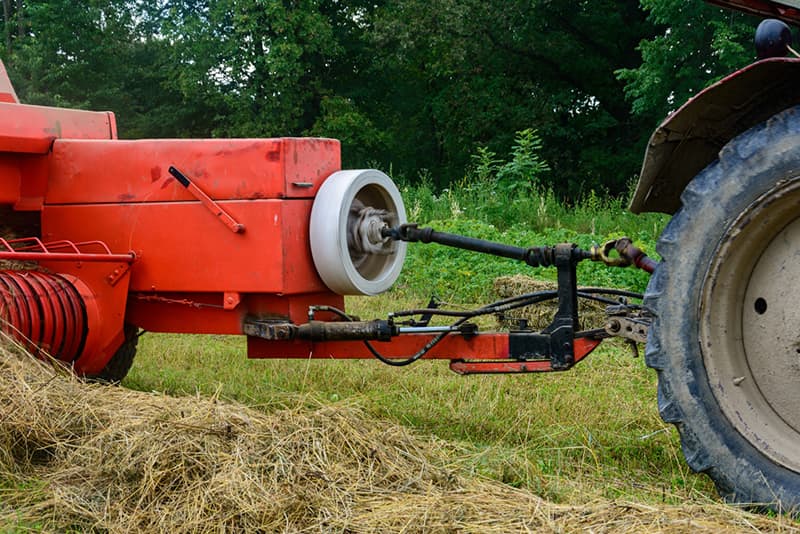
With spring harvest coming up, now is the best time to review how to maintain your PTO driveline to extend its longevity and prevent failure. We know it’s tempting to take shortcuts, but neglecting to inspect your farm equipment can lead to hazardous outcomes and costly repairs. A routine tractor PTO driveline maintenance plan can help you avoid any risks to your farming operations.
Tractor driveline maintenance: visual inspection checks and operator safety
How often should you perform maintenance on your tractor?
You should conduct a visual inspection of your driveline components (joints, shafts, couplings, guards, etc.) every time you start your tractor. This will help you detect wear and tear, loose parts, or safety hazards before you start your equipment.
How to conduct a visual inspection on your PTO driveline
Start by looking at the driveline guard. This is the outer shell or covering surrounding the rotating shaft and joints of the driveline. When the guard is properly attached and the bearings are in operating condition, it will spin freely and separately from the PTO shaft. The guard not only keeps the driveline clean, but also is a key safety feature that prevents items from getting caught by a rotating driveline, such as ropes or your clothes.
You’ll want to look for any wear that causes looseness in any of the joints and guards. We recommend replacing broken guards immediately. Guards should be in place and need to freely rotate. While it may be tempting to leave the guards off your equipment for easier access to the driveline, guards should always be installed and functional for safety. It is very common for farmers to remove the guards because they want easier access for maintenance, but this has led to countless injuries. It’s very important for both your safety and the integrity of the equipment to keep the guard in place.
After you’ve inspected your driveline components, give your PTO connection a nice shake to make sure everything is tight. While you’re inspecting your driveline, we recommend inspecting the 3-point hitch lift arms, top link, pins, balls, and sockets for proper installation and signs of wear as well.
Tractor driveline maintenance is all about greasing
When we say grease, we mean an EP grease lubricant meeting the NLGI number 2 specification. Most components require an 8-hour lubrication service interval for routine tractor driveline maintenance—meaning after 8 hours of operation, grease everything. This might vary depending on the style and design of the shaft. There are recommended amounts of lubrication for each component that gets greased. You must always lubricate universal joints, constant velocity joints, and the telescoping members (inner and outer shafts which are hidden by the plastic shield). The way these driveline components are lubricated differs from one design to the other. It’s important to note that while you can’t over grease a PTO driveline, failing to wipe excess grease from the exterior of a universal joint can cause dirt and debris to build up on your equipment.
Consult your equipment owner's manual for the specific intervals and maintenance requirements for your equipment.
Image Source: Courtesy of Weasler®
How often should you grease a PTO shaft?
A good rule of thumb is to grease your equipment after 8 hours of use. If you don’t use your equipment often, you still need to keep it greased. For a smaller piece of equipment that is only used a couple times a year, grease it before each use or annually to maintain the integrity of the equipment. If you cannot find greasing information on the safety shields, the rule of thumb is to pump until you see fresh grease coming out of the joints.
These pictures show examples of damage caused by lack of grease on a 50° constant velocity joint ball and socket.
Image Source: Courtesy of Weasler®
Helpful resources for Weasler® components and kits
Weasler® Drive Shaft Lubricating Procedure
Weasler E-Kit Features and Benefits - YouTube
North American vs Metric Style Drivelines
A North American driveline will typically have a telescoping square, rectangular, or blind shaft inside a round tube with a slip sleeve that contains a grease coupling.
Metric-style drivelines have telescoping shafts identified by the star, lemon, or bell shape of the tube. These driveline components must be completely disassembled. First, you must remove the inner from the outer, grease the inner tube, and then reassemble.
Need more detail on different style drivelines?
Learn more about the differences between North American vs Metric Style Drivelines.
View North American Universal Joint ratings
View Metric Universal Joint ratings
Weasler® parts and maintenance downloads
A routine checklist for tractor driveline maintenance
Tractor driveline maintenance is all about visual inspection and lubrication. Before every use and on a routine basis throughout the farming season, be sure to take your time and inspect your equipment.
Here are the best practices for routine driveline inspection and maintenance.
- Always turn off your tractor and remove the keys.
- Remove the driveline from the tractor/implement for maintenance.
- Remove the guards from the PTO shaft.
- Clean the driveline to remove dirt and debris for inspection.
- Inspect the driveline for any failures such as cracks, loose joints, and other signs of wear.
- Disassemble the two telescoping members of the shaft.
- Grease the shafts and tube (also called telescoping members).
- Grease universal joints (also called cardan joints and cross and bearing kits).
- Grease double cardan or constant velocity joints and center sections.
- Reinstall your safety shield (guard) and lubricate guard bearings.
DO NOT operate the equipment without safety shields in place.
What causes tractor driveline failure?
Three of the most common causes of PTO driveline failure include. . .
- Operating over the designed operating angles
- Lack of grease / lubrication
- Operating above the designed horsepower rating
Shop our agricultural and grease products
Royal Brass & Hose offers the original, aftermarket, and OEM industrial parts for your farming equipment and agricultural implements. We stock quality products for replacement parts for your three-point hitches, bale spears, tractors, combines, cultivators, and more.
Need help with your agricultural driveline?
We’re experts in agricultural drivelines. Talk to one of our trusted tech service or sales reps today for help choosing the right products for your driveline repairs. Contact us or call 800-669-9650 to speak with a member of our Customer Service team at any of our 11 locations (Knoxville, TN; Marietta, GA; Orlando, FL; Charlotte, NC; Little Rock, AR; Fort Worth, TX; Benton, IL; Madisonville, KY; Princeton, WV; Birmingham, AL; Calvert City, KY).