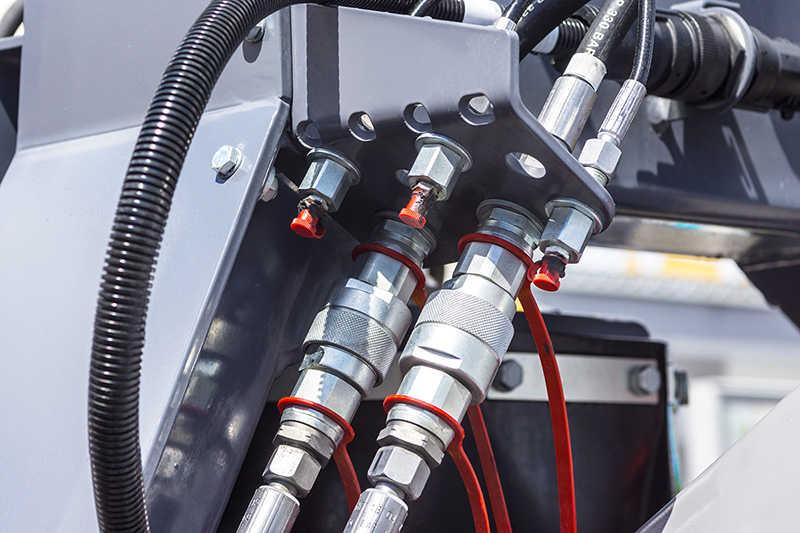
Types of Quick Disconnects
Quick disconnects, or quick couplings, are used for connecting and disconnecting fluid lines quickly and efficiently. However, it’s common to see them used in the wrong application. This guide will cover the most frequent misapplications of quick disconnects and their solutions.
-
Hydraulic Quick Disconnects: Designed for high-pressure applications, these are commonly used in hydraulic systems of construction equipment, agricultural machinery, and industrial machinery.
-
Pneumatic Quick Disconnects: Suited for air pressure systems, they are often found in manufacturing settings for connecting air tools and equipment.
-
OEM Quick Disconnects: These are custom designed for specific equipment by original equipment manufacturers (OEMs), ensuring compatibility and optimal performance with their branded equipment.
Read more on The Basics of Quick Disconnects.
Quick Disconnect Misapplications and Solutions
Over time, we’ve seen numerous misuses of quick disconnects in the field. Here are the most common occurrences and how to ensure you’re using your quick disconnect fittings properly.
1. Misunderstanding Pressure Ratings
Issue: Using fittings that don't align with the system's pressure requirements, risking leaks or bursts. This often occurs due to overlooking the system's peak pressure levels or misinterpreting pressure specifications.
Solution: Carefully select fittings with pressure ratings that exceed or match the system's maximum pressure. Always verify the peak pressure demands of the system before choosing the fittings.
2. Air Flow Constraints in Pneumatic Systems
Issue: Choosing quick disconnects that restrict air flow results in decreased efficiency. This problem arises when the diameter of the disconnects is not adequately matched with the air system's requirements.
Solution: Opt for quick disconnects designed to sustain required air flow levels for optimal tool performance. Consider both the diameter and the design of the disconnects to ensure they facilitate sufficient air flow.
3. Mismatch of Materials for Specific Operational Environments in OEM Parts
Issue: Utilizing materials in OEM (Original Equipment Manufacturer) parts that are inappropriate for the specific operational environments can lead to early deterioration caused by environmental factors like corrosion, extreme temperatures, or chemical exposure.
Solution: Select materials for OEM parts that are resilient to the environmental conditions, with an emphasis on corrosion resistance and temperature tolerance. The choice of materials should be made after a detailed evaluation of the operational environment.
4. Flawed Connection/Disconnection Techniques
Issue: Incorrect handling of the quick disconnects can lead to premature wear. This often occurs due to a lack of understanding of the proper techniques or hurried operations.
Solution: Implement training programs focused on the correct handling and maintenance procedures for quick disconnects.
5. Neglecting Maintenance
Issue: Lack of regular inspections and maintenance leads to unnoticed wear and tear. This negligence can result in unexpected system failures or safety hazards.
Solution: Establish a comprehensive maintenance routine to ensure durability and reliability. Maintenance should include regular inspections, cleaning, and immediate replacement of worn parts.
6. Misuse in Vibrating Environments
Issue: Quick disconnects used in high-vibration settings can suffer surface corrosion or damage, also known as brinelling. This is caused by the repetitive impact and stress in such environments.
Solution: Employ whip hoses or threaded quick connects for enhanced durability. These solutions help to absorb or distribute the vibrational forces more effectively.
7. Side Load Damage
Issue: Side loading causes damage to the coupling sleeve and valve. This damage is a result of applying force in a direction that the coupling is not designed to handle.
Solution: Install quick disconnects in a manner that aligns with the direction of the load to prevent mechanical stress. Proper alignment ensures the load is evenly distributed across the coupling.
8. Contamination Concerns
Issue: Dirt and debris accumulation can lead to coupling damage.
Solution: Regularly use and maintain dust caps and plugs and ensure cleanliness before connecting. This includes both storing disconnects in clean environments and cleaning them before use.
9. Rotation-Related Failures
Issue: Full rotational movement can cause unintended disconnections.
Solution: Utilize swivel joints where full rotational movement is necessary to prevent accidental disengagement.
10. Inappropriate Pressure Release
Issue: Use of improper methods like hammering for pressure release can cause severe damage to the fittings.
Solution: Adopt thread-together options* for applications involving high pressure, ensuring safe and controlled connection/disconnection.
*"Thread-together techniques" refer to a method of connecting and disconnecting components in a system where the parts are designed to be screwed together or unscrewed (threaded) manually. This contrasts with other methods like quick-release couplings or snap-fit connections.
11. Material Compatibility
Issue: If the material of the quick disconnect is incompatible with the working fluid or operational temperatures, this can cause material failure.
Solution: Select quick disconnect fitting materials based on comprehensive compatibility with fluids and operational temperature ranges.
12. Valving Configuration Errors
Issue: Selecting an inappropriate valving configuration for the specific system requirements can lead to poor control of fluid or gas flow within the system. This inefficiency can affect the performance of the entire system, causing it to operate below optimal levels.
Solution: Determine the necessity of single or double shut-off, non-shutoff, and dry-break configurations based on the system’s operational needs.
13. Overlooking Pressure and Flow Dynamics
Issue: Failure to match the quick disconnect’s pressure rating and flow requirements with the system.
Solution: Ensure that the quick disconnect’s pressure rating and effective orifice rating align with the system’s pressure and flow demands.
14. Precision Issues in Ball & Sleeve Lock Couplings
Issue: Inconsistent connections in the ball and sleeve lock mechanism can lead to imperfect seals, resulting in leaks. This not only leads to the loss of fluids or gases but also poses safety and environmental risks, especially if the substances are hazardous.
Solution: Use precision-grade balls in couplings and select materials like stainless steel or brass based on fluid characteristics.
Troubleshooting Techniques for Quick Disconnect Issues
-
Flow and Pressure Testing: Regularly test the flow and pressure through the quick disconnects to ensure they meet system requirements.
-
Thermal Inspection: Use thermal imaging to detect unusual heat signatures that may indicate internal leakage or blockages.
-
Acoustic Analysis: Listen for unusual sounds that might indicate internal damage or malfunction within the quick disconnect.
-
Diagnostic Equipment: Utilize diagnostic tools designed for hydraulic and pneumatic systems to identify issues such as internal leakage or pressure fluctuations.
-
Unexpected Disconnection: Ensure that the coupling is correctly locked and that there is no excessive force or pressure causing the disconnection.
Conclusion
Addressing these specific misapplications can significantly improve the performance and safety of quick disconnect systems in hydraulic, pneumatic, and OEM applications. By selecting the appropriate fittings, understanding their operational nuances, and maintaining them meticulously, system reliability can be greatly enhanced.
For more information, download our Royal Brass and Hose Quick Disconnect Book.
Need help with your quick disconnects?
When it comes to quick disconnects, we’re trusted experts. Contact us or call 1-800-669-9650 to speak with a member of our customer service team at any of our 11 locations (Knoxville, TN; Marietta, GA; Orlando, FL; Charlotte, NC; Little Rock, AR; Fort Worth, TX; Benton, IL; Madisonville, KY; Princeton, WV; Birmingham, AL; Calvert City, KY).